About the INSIDE series
This series takes a deep dive inside our teams to take a look at how we work and discover our culture behind the scenes.
Today, we take a close look at our mechanical engineering team, led by Sébastien Cossette for the past ten years.
After graduating from the Polytechnique School of Montreal in mechanical engineering, Sébastien Cossette joined CLEIO in 2013 with a background in product development, along with industrial designer François Gélinas. “At that time, CLEIO was dealing with different consultants for mechanical development and industrial design, but the goal was to bring these services in-house. That’s when François and I heard about CLEIO”, he says.
They started with two small teams in mechanical engineering and industrial design “In the first four months, we were four. We did a little bit of everything: recruiting, project management, meeting with clients, evaluation, technical sales”. Since then, our company has considerably grown, integrating new disciplines and increasing from about 20 employees to nearly 80 by the beginning of 2023.
Sébastien and François
A team that is constantly learning and evolving
Stepping out of the comfort zone
His goal is to help the mechanical engineering team to grow so that they can provide technical leadership. “Technical leadership is about making the right decisions on projects. It’s more than just execution”, he explains.
Achieving this result is all about project assignment: “I’m not going to throw someone into something completely new, but I’m also not going to keep them in only what they know how to do”, he continues. And it works. Alex joined CLEIO nine months ago, and he already feels he’s learned a lot, especially about the steps of bringing a product into production.
Alex
Achieving versatile tasks
The wide variety of projects is another great asset for a mechanical engineer who wants to broaden his knowledge. “With us, mechanical engineers know that they will work on projects on which they will touch many things and learn from it”, says Sébastien.
That’s what appealed to Louis when he decided to join CLEIO five and a half years ago. “You do five and a half years at CLEIO and five and a half years in a more standard company: you don’t come out with the same baggage. It’s much richer”, he admits.
One of our particularities is the multidisciplinarity of our team. Throughout a project, mechanical engineers collaborate with designers, electronic engineers, software developers, and quality assurance experts. Everyone knows the strengths of others and how to work with them to get the desired results.
“We know we make one together. We complement each other across departments. Yes, mechanical engineering is crucial, but our work wouldn’t make sense without the design and strategy experts, for example. My team is more than the mechanical engineering group. It’s everyone else too. No silos at CLEIO: just transparency between each expertise. An openness to other approaches, and above all, to different ways of doing things”
— Sébastien
Projects with their own set of challenges
CLEIO works on promising projects, primarily concentrated in the medical industry. What drives us is the idea of making a significant difference in people’s health through thinking and innovating under one roof. For Louis, it is also the assurance of not falling into a routine by working on always different projects.
“The type of projects often change. There is always a little extra challenge to look for, and that’s what keeps me motivated week after week”
— Louis
As we write these lines, our mechanical engineering team has about 15 new projects underway. “There are seven to eight projects that are in a major development period, but there are at least as many that are providing maintenance and support to past customers”, says Sébastien.
These projects bring their own challenges, mainly because the manufacturing processes are very diversified (thermoforming, sheet metal, plastic injection, glass, and carbon fiber molding) and because the device’s location imposes constraints. “There’s a difference in making a device that’s going to be on wheels and a device that’s going to be set up in an hospital and fixed to the floor”, Sébastien adds.
A matter of culture
Making everyone comfortable
“It’s not just words on a website”, Sébastien says. “I’m really receptive to making people feel good. When I feel some discomfort, I need to be able to talk about it”. When a mistake has been made, he doesn’t look for someone to blame: “I try to understand where we went wrong as a team. It’s easier after that to improve ourselves”.
Sébastien acquired his penchant for communication and openness over time, inspired by the trusting relationship he developed with our CEO, Alexis Bilodeau: “He’s someone I feel really comfortable saying what I like and what I don’t like. That’s something I try to have in the relationship with people on my team”.
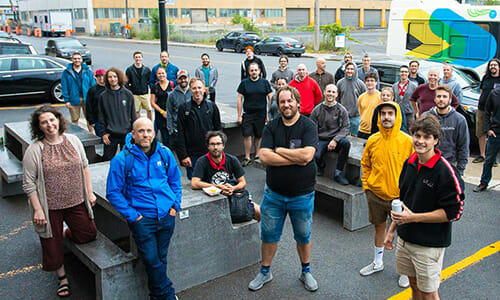
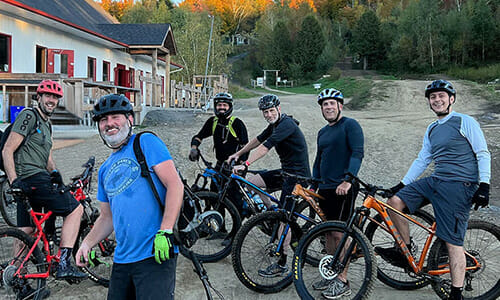
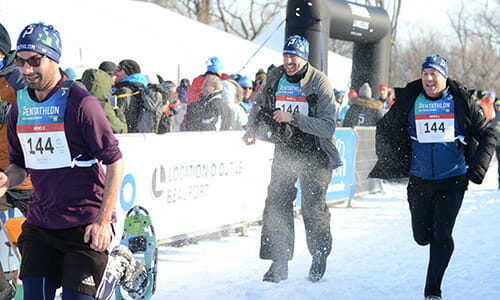
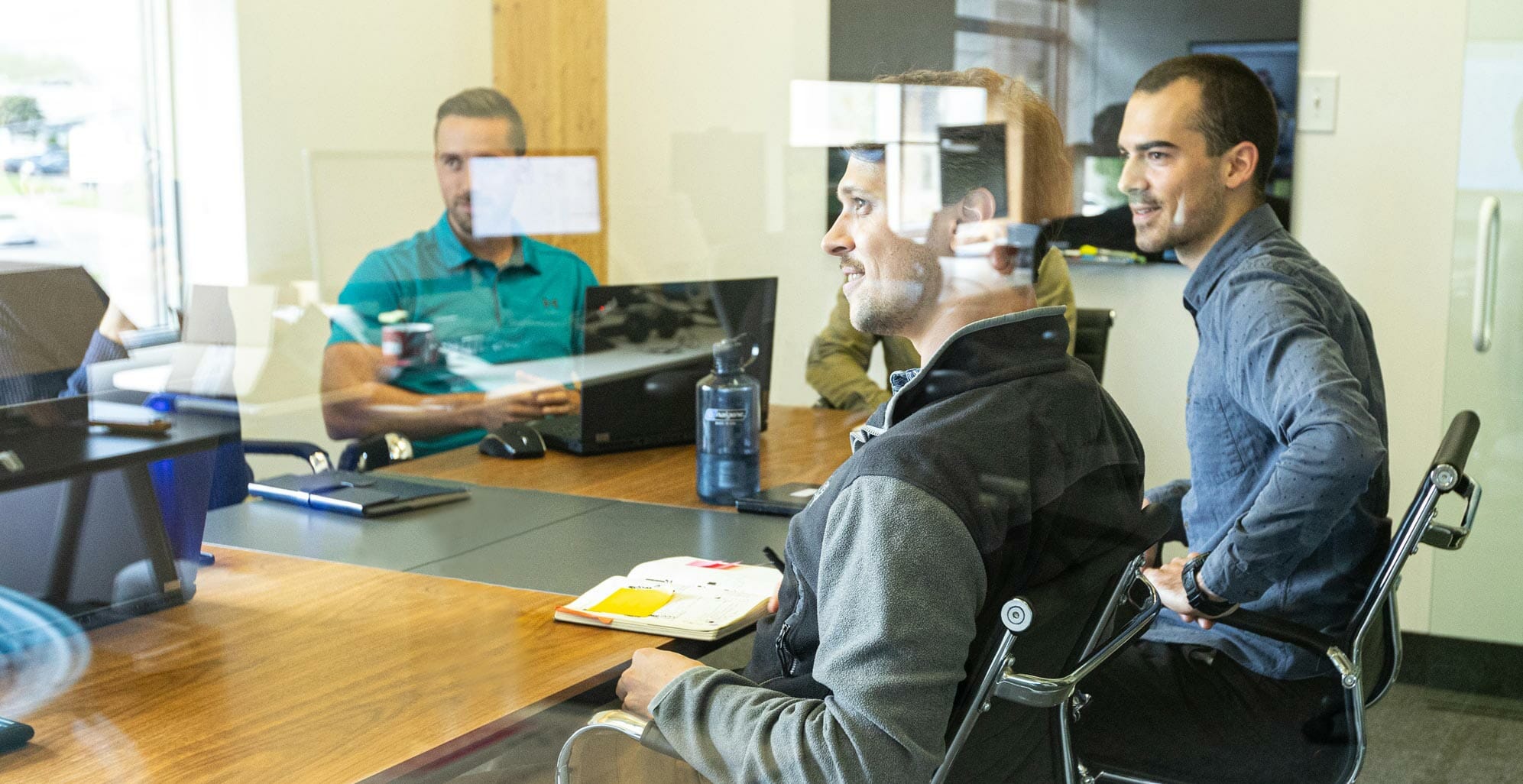
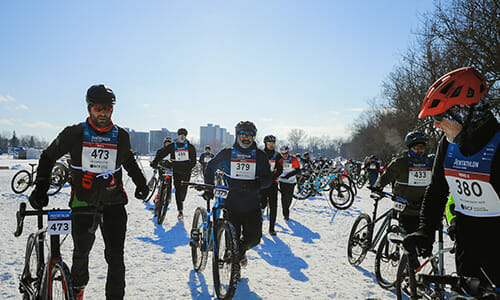
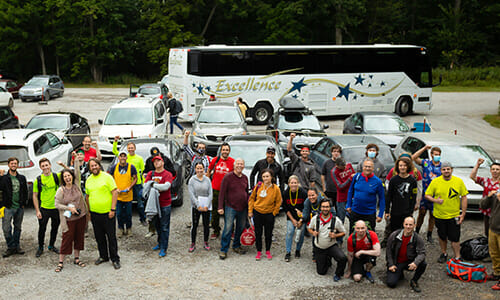
Encouraging team spirit
Every two weeks, Sébastien brings his entire team together at the Laval office so that everyone can share their knowledge or difficulties. It’s an opportunity to talk about the issues and challenges of a project that are unknown to the rest of the team, but also a good way to easily find resourceful people to help solve a problem encountered.
These meetings are very appreciated, as Alex explains: “It helps to have a good team spirit. We help each other, and we talk a lot”.
The atmosphere within the team is good. More and more people like to come to work at the office, and it’s common to have activities outside of work time. “It could be a happy hour or a bike ride. All it takes is someone with a good idea, and we go with it. Often, everyone is eager to go and get together to do something other than work”, Louis says enthusiastically.
What’s next?
However, he plans to refine his recruitment method. Until now, he was looking for people with very similar profiles because they often worked alone on a project: “I needed jacks-of-all-trades people with a very strong creative side, who could communicate easily with the client”, he explains.
Today, he wants to put more emphasis on rigor by hiring engineers who will be able to properly document projects and tests: “As the company is growing, we will have bigger projects. I can afford to pair someone a little more creative with someone a little more rigorous”.
Spotlight
Sébastien
- Seniority at CLEIO: 10 years
- Personal interests: Sports (hockey, mountain biking, road biking, running, cross-country skiing), family, travel, renovation
- What drives him: Putting people comfortable and making them grow
Louis
- Seniority at CLEIO: almost 6 years
- Personal interests: Hockey, home improvement, music
- What drives him: Taking on new challenges
Alex
- Seniority at CLEIO: 9 months
- Personal interests: Sports (cycling, cross-country skiing, hockey, ice skating, climbing), cooking
- What drives him: Being a jack of all trades
Looking for a life-changing job experience?
If you’re currently looking for a new professional adventure and challenges, it might be a good time to send us your application to join CLEIO’s team!